Überlegene Folienqualität bei höchster Liniengeschwindigkeit – DORNIER Folienreckanlagen
DORNIER ist der zuverlässige Partner für alle Anforderungen rund um die Herstellung anwendungsspezifischer Anlagen für die Produktion von Folien (Polyester, Polypropylen, Polyamid, PEN u.v.a.m.). Ob Einzelkomponenten oder schlüsselfertige Gesamtanlagen nach Kundenwunsch: DORNIER konstruiert, entwirft und baut alles aus einer Hand.
Produkte
Anwendungen
Die vielseitigen Einsatzbereiche unserer Folienreckanlagen
DORNIER Folienreckanlagen sind darauf ausgelegt, höchste Flexibilität und Präzision für eine Vielzahl von Anwendungen zu bieten. Sie zeichnen sich durch ihre Vielseitigkeit und Zuverlässigkeit aus und erfüllen die anspruchsvollsten Anforderungen verschiedenster Industrien auf der ganzen Welt. Dank modernster Technologie und innovativer Konstruktionslösungen ermöglichen unsere Anlagen eine effiziente und qualitativ hochwertige Produktion bei gleichzeitig maximaler Anpassungsfähigkeit an individuelle Bedürfnisse. Unabhängig von den spezifischen Anforderungen Ihrer Branche – DORNIER Folienreckanlagen stehen für Fortschritt, Leistungsfähigkeit und Zukunftssicherheit. Entdecken Sie, wie unsere Technologien dazu beitragen können, Ihre Produktionsprozesse auf ein neues Niveau zu heben und Ihre Wettbewerbsfähigkeit nachhaltig zu stärken.
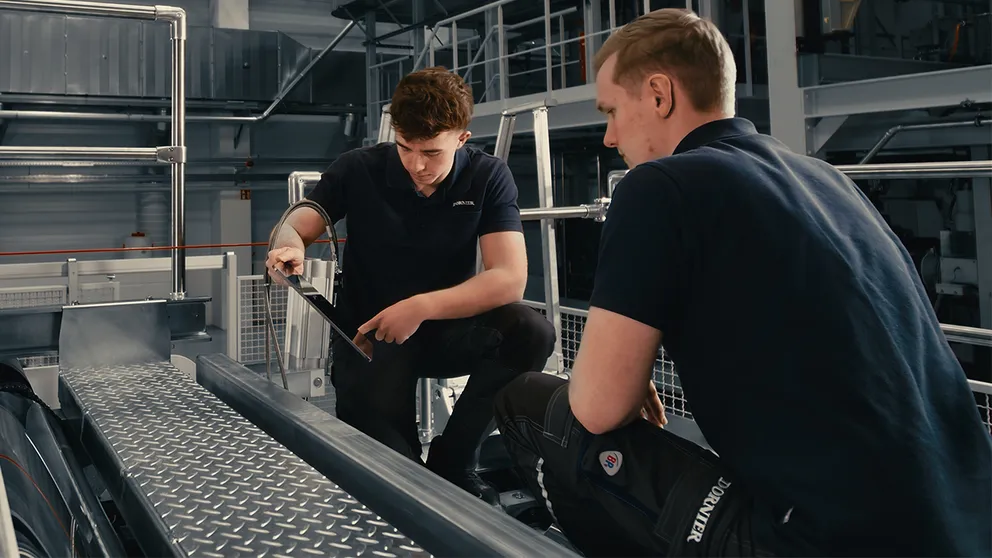
Weltweiter Service
Das Service-Team aus Lindau steht Ihnen bereits vor dem Kauf Ihrer Anlage beratend zur Seite und unterstützt Sie bei der Montage, Inbetriebnahme, Wartung sowie der Schulung Ihrer Mitarbeiter. Darüber hinaus bietet DORNIER in allen wichtigen Absatzmärkten Service- und Verkaufsniederlassungen, um eine schnelle und direkte Kontaktaufnahme vor Ort zu gewährleisten.